Dependable Steel Fixing Providers: Guaranteeing Architectural Integrity
Dependable Steel Fixing Providers: Guaranteeing Architectural Integrity
Blog Article
Innovative Patterns in Steel Construction: Enhancing Longevity and Accuracy
In the realm of steel construction, the pursuit of longevity and accuracy has actually brought about a wave of cutting-edge patterns that are reshaping the sector. From advancements in welding technologies to the assimilation of robotic automation in fabrication processes, the landscape of steel production is developing swiftly. High-strength alloy advancement, coupled with the usage of 3D modeling and simulation software application, is pressing the borders of what is achievable in regards to structural integrity and accuracy. Moreover, the expanding emphasis on sustainable techniques in steel manufacturing is not just driving performance but likewise cultivating a more environmentally aware method to manufacture. These patterns are not just forming the here and now but additionally preparing for the future of steel fabrication, promising more improvements in longevity and precision.
Advanced Welding Technologies
In the realm of steel fabrication, the fostering of innovative welding innovations has actually considerably transformed the market's technique to attaining remarkable top quality and accuracy in architectural welds. Advanced welding innovations, such as laser light beam welding and rubbing mix welding, have become game-changers in the area. Laser light beam welding utilizes a focused laser beam of light to sign up with metal components with exceptional precision and speed, making it optimal for slim materials and intricate designs. On the other hand, rubbing stir welding develops incredibly solid bonds by mechanically intermixing the particles of the materials at the joint, removing the demand for thawing the steel. These modern technologies offer various advantages, including reduced heat-affected areas, marginal distortion, and enhanced mechanical properties in the bonded joints. By leveraging these advanced welding techniques, steel fabricators can boost the resilience, strength, and accuracy of their structural welds, fulfilling the significantly requiring needs of modern-day building and construction tasks.
Robotic Automation in Manufacture
Accepting robot automation has actually ended up being a foundation of modern steel fabrication techniques, boosting and simplifying processes efficiency throughout the industry. Robotics are changing the means steel parts are produced, using unequaled accuracy and rate while lowering human mistake. These automated systems can take care of repeated tasks with regular accuracy, causing higher quality final product.
One key benefit of robotic automation in steel fabrication is the ability to function all the time without tiredness, considerably increasing production outcome. This continuous operation lessens downtime and increases task timelines, eventually conserving prices for manufacturers. Additionally, robots can be set to do complex jobs that may be unsafe or challenging for human workers, boosting safety and security in the office.
In addition, robotic automation allows smooth assimilation with other electronic modern technologies, such as computer-aided layout (CAD) software and Internet of Points (IoT) systems (steel fabrication melbourne). This interconnected method improves interaction between various phases of fabrication, maximizing operations and making certain real-time surveillance and control. As the steel manufacture sector proceeds to evolve, robotic automation attracts attention as a transformative pressure driving effectiveness and precision in manufacturing procedures
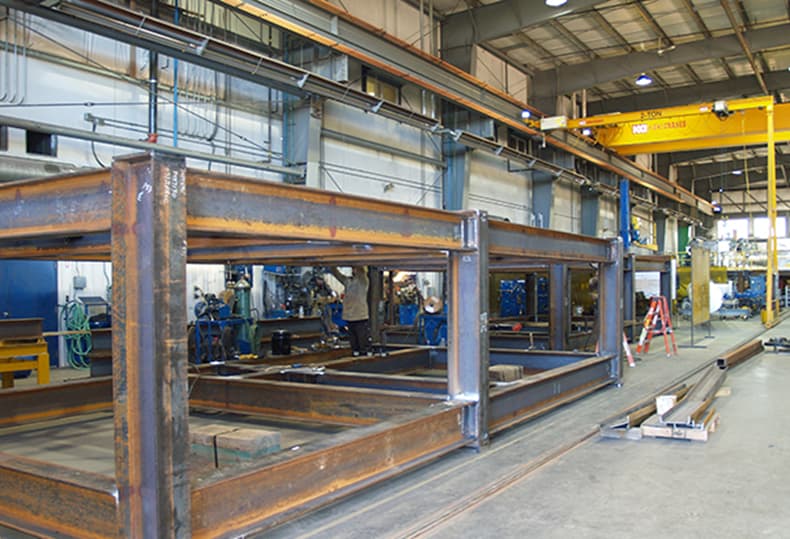
High-Strength Alloy Growth
The advancement of high-strength alloy development in steel construction is improving the industry's technique to improving product toughness and efficiency. High-strength alloys are crafted to exhibit premium mechanical residential or commercial properties, such as raised tensile toughness, durability, and rust resistance contrasted to traditional steel qualities. By including these innovative alloys right into manufacture procedures, manufacturers can create elements that hold up against higher stress levels and extreme settings, causing even more durable and reputable end products.
One trick advantage of high-strength alloy growth is the ability to lower material thickness without compromising structural honesty. This not just leads to lighter-weight parts however likewise adds to cost savings and enhanced efficiency in manufacture and setting up processes. Moreover, the improved strength-to-weight proportion of these alloys allows for the layout and construction of structures with greater load-bearing capacities while lessening total weight.
3D Modeling and Simulation Software
Innovations in steel manufacture procedures have actually been considerably propelled by the combination of sophisticated 3D modeling and simulation software tools. These devices permit makers to develop in-depth online versions of their jobs, enabling them to imagine the end product with precision before any kind of manual labor starts. By simulating various anxiety factors, environmental conditions, and structural loads, fabricators can maximize styles for enhanced longevity and performance. Furthermore, 3D modeling and simulation software improve the production procedure by determining prospective issues early on, decreasing the need for expensive rework and minimizing product waste.
Lasting Practices in Steel Manufacturing
Incorporating lasting practices into steel manufacturing procedures is vital for minimizing environmental impact and making sure lasting source schedule. One key lasting practice is the fostering of energy-efficient modern technologies to decrease greenhouse gas exhausts during the steel production process. This consists of making use of renewable resource sources, such as solar or wind power, to power steel plants and applying energy-efficient tools to enhance energy usage.
One more vital aspect of sustainable steel production is the accountable sourcing of resources. This includes guaranteeing that the iron ore and other sources utilized in steelmaking are acquired from honest and environmentally pleasant resources. By advertising openness in the supply chain and sticking to stringent ecological criteria, steel manufacturers can lessen the adverse influences of resource removal on regional ecosystems and neighborhoods.

Conclusion
To conclude, the ingenious patterns in steel fabrication click here for more such as advanced welding modern technologies, robot automation, high-strength alloy growth, 3D modeling and simulation software, and lasting methods are improving the longevity and accuracy of steel products. These innovations are reinventing the steel manufacture sector by improving efficiency, top quality, and sustainability. It is clear that the future of steel fabrication hinges on welcoming these cutting-edge modern technologies to meet the demands of modern building and manufacturing sectors.
In the realm of steel manufacture, the search of sturdiness and precision has actually led to a wave of innovative fads that are improving the industry.In the world of steel fabrication, the fostering of innovative welding innovations has considerably changed the sector's strategy to achieving premium high quality and accuracy in architectural welds. As the steel manufacture market proceeds to evolve, robotic automation stands out as a transformative pressure driving efficiency and accuracy in making processes.
In addition, reusing and recycling steel scrap and waste products play a considerable duty in boosting the sustainability of steel manufacturing. metal fabrication melbourne.In conclusion, the cutting-edge fads in steel fabrication such as innovative welding modern technologies, robot view it automation, high-strength alloy advancement, 3D modeling and simulation software program, and lasting techniques are boosting the durability and precision of steel products
Report this page